What are RTD Sensors?
Discover the world of RTD sensors with DXM. RTD sensor, known as Resistance Temperature Detector, offer precise temperature measurement, making them essential for various industrial applications. At DXM, we excel in providing high-quality RTD sensor that ensure accuracy and reliability. Our expert designs cater to diverse needs, supporting optimal performance and efficiency. Trust DXM for innovative solutions in temperature sensing technology. Explore our range of RTD sensors to enhance your operational capabilities.
- Understanding RTD Sensors: Precision, Reliability, and Versatility Explained
- Types of RTD Sensors and Their Impact on Accuracy
- Two key factors influence the accuracy of RTD sensor:
- RTD Sensors: Standardization and Tolerance in Temperature Measurement
- DIN Standard Specifications for RTD Sensor
- Tolerance Classifications for RTD Sensors
- How does a RTD Sensor work?
- RTD Sensors: Connection Configurations and Their Impact on Accuracy
- Two-Wire Configuration
- Three-Wire Configuration
- Four-Wire Configuration
- The Impact of Lead Resistance on RTD Sensors
- Practical Considerations for Implementing RTD Sensor
- Conclusion: Maximizing Accuracy with RTD Sensors
RTD sensors, or Resistance Temperature Detectors, are highly accurate temperature sensors widely used across various industries. So, what are RTD sensors? These RTD sensors are renowned for their precision, reliability, and versatility, making the RTD Sensor a top choice for accurate temperature measurement across industries.
RTD sensors operate on a fundamental principle: the resistance of a material, typically platinum, increases predictably with temperature. This predictable change allows for accurate temperature measurements.
Unlike active sensors, RTD sensors are passive devices. They do not generate their own electrical signal. Instead, they require an external circuit to measure resistance changes and convert them into temperature readings.
DXM trusted by resistance temperature detector manufacturer, RTD sensors are essential in applications demanding precise temperature monitoring. This article explores what RTD sensors are, their operating principles, types, and practical considerations for effective use.
Types of RTD Sensors and Their Impact on Accuracy
When exploring what RTD sensors are, it’s essential to understand that they come in different types, each based on the material used for the sensing element. These materials offer unique benefits depending on the specific needs of your application.
-
Platinum RTD Sensor (Pt100, Pt1000): These are the most popular RTD sensors. They are known for their excellent stability, accuracy, and wide temperature range (-200°C to +850°C). Platinum is also resistant to corrosion, making these sensors perfect for critical applications.
-
Nickel RTD Sensor: These are more affordable than platinum RTDs but have a smaller temperature range (-80°C to +260°C). Nickel RTDs might lose accuracy over time, so they are best for less demanding uses.
-
Copper RTD Sensor : Copper RTDs are cost-effective and offer good linearity. However, they work best at lower temperatures and can oxidize at higher ones, which can affect their accuracy.
-
Two key factors influence the accuracy of RTD sensor:
-
Reference Resistance Tolerance: For Pt100 sensors, the reference resistance is 100 ohms at 0°C. This sets the baseline for accuracy.
-
Temperature Coefficient Precision: This ensures a consistent and linear response across a wide temperature range, which is crucial for accurate measurements.
High-grade platinum and strict manufacturing controls lead to RTD sensor with exceptional accuracy. However, this comes at a higher cost. These considerations are vital for resistance temperature detector manufacturers when explaining what RTD sensors are and their suitability for various applications.
RTD Sensors: Standardization and Tolerance in Temperature Measurement
RTD sensors, widely used for precise temperature measurement, follow standardized resistance-temperature relationships, ensuring accuracy and reliability. The most common standard is the DIN curve, defined by DIN EN 60751, which is widely adopted by resistance temperature detector manufacturers.
DIN Standard Specifications for RTD Sensor
RTD sensors typically have a reference resistance of 100 ohms at 0°C. The standard temperature coefficient is 0.00385 ohms/ohm/°C. This means the resistance increases by 0.385 ohms for every degree Celsius rise in temperature.
Tolerance Classifications for RTD Sensors
RTD sensors are categorized into different tolerance classes, defining the maximum allowable deviation from the standard curve:
- DIN Class A: ±(0.15 + 0.002 |T|°C)
- DIN Class B: ±(0.3 + 0.005 |T|°C)
- DIN Class C: ±(1.2 + 0.005 |T|°C)
In these formulas, |T| represents the absolute temperature in degrees Celsius. Class A RTD sensors are ideal for high-precision applications, while Class B and Class C are suitable for less critical uses.
How does a RTD Sensor work?
RTD sensors operate on a fundamental principle: the electrical resistance of certain materials changes predictably with temperature. RTD sensor capitalizes on this, as their resistance increases with rising temperatures, enabling precise temperature measurements.
Unlike active sensors like thermocouples, RTD sensors are passive devices. They do not generate their own electrical signal. Instead, external circuitry is required to measure the resistance, which is then converted into a corresponding temperature reading.
Platinum RTDs are the most common type, known for their accuracy and repeatability across various conditions. These RTD sensors, including the widely used PT100, feature metals like platinum, copper, or nickel. The PT100, for instance, has a resistance of 100 ohms at 0°C, making it ideal for applications requiring consistent temperature control.
RTD Sensors: Connection Configurations and Their Impact on Accuracy
RTD sensor can be connected in various wiring configurations, each affecting the accuracy of temperature measurements. The choice of configuration depends on the application's accuracy requirements and the capabilities of the measuring instrument.
Two-Wire Configuration
This is the simplest and most cost-effective setup, where two wires connect the RTD sensor to the measuring instrument. However, it is prone to errors due to lead wire resistance, especially over long distances, which can significantly impact the measurement accuracy.
Three-Wire Configuration
The three-wire setup is the most common in industrial applications. It introduces a third wire that helps compensate for lead resistance, offering a good balance between accuracy and complexity. This configuration reduces the error introduced by the wiring, making it reliable for most industrial uses.
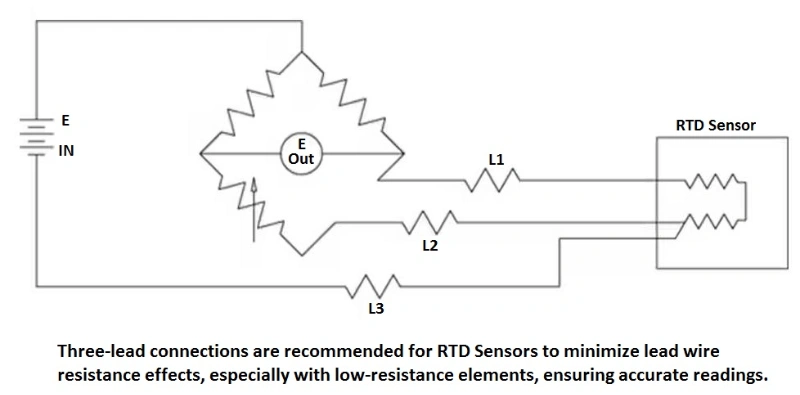
Four-Wire Configuration
For the highest accuracy, the four-wire configuration is used. It employs two pairs of wires: one pair supplies the excitation current, and the other measures the voltage drop across the RTD sensor. This method effectively eliminates the influence of lead resistance, but it may not be supported by all industrial controllers.
The Impact of Lead Resistance on RTD Sensors
RTD sensors are sensitive to lead resistance, which can introduce significant errors in temperature measurements, particularly in two-wire configurations or with long cable runs. For instance, copper wire typically has a resistance of about 10.4 ohms per 1000 feet at 20°C. In a two-wire setup, this resistance adds to the RTD sensor’s resistance, leading to a positive error in temperature readings.
The three-wire configuration mitigates this issue by using a third wire to measure and partially compensate for lead resistance. This reduces the error caused by the leads, making the measurement more accurate.
For the highest accuracy, the four-wire configuration completely eliminates the impact of lead resistance. By separating the current-carrying and voltage-sensing wires, this setup ensures precise temperature readings, which is crucial for laboratory environments and critical applications.
Practical Considerations for Implementing RTD Sensor
When selecting and implementing RTD sensors, consider these key factors:
-
Temperature Range: Ensure the RTD sensor is suitable for the application's expected temperature range.
-
Environmental Conditions: Evaluate factors like vibration, chemical exposure, and moisture that could impact the RTD sensor’s performance and longevity.
-
Response Time: For applications requiring rapid temperature measurements, consider the thermal mass and design of the RTD sensor assembly.
-
Self-Heating: The current used to measure the RTD sensor's resistance can cause minimal heating, which should be considered in high-precision applications.
-
Calibration: Regular calibration is crucial to maintain accuracy, particularly in critical applications.
-
Conclusion: Maximizing Accuracy with RTD Sensors
RTD sensors are essential tools for precise temperature measurement across diverse applications. Their standardized performance, multiple configurations, and high accuracy make them a preferred choice for industrial and scientific needs.
The accuracy of RTD sensor depends on factors such as the type of element used (e.g., platinum 100-ohm RTD), the class of tolerance, and the wiring configuration. Selecting the correct RTD sensor involves considering the required precision, environmental conditions, and compatibility with instrumentation.
Connection configurations, like three-wire or four-wire setups, play a crucial role in minimizing errors caused by lead resistance. This ensures accurate temperature readings, particularly in industrial settings where precision is paramount. By understanding what is RTD sensor and how they function, engineers and technicians can optimize their temperature measurement systems for reliable and consistent performance.
Recommended for you
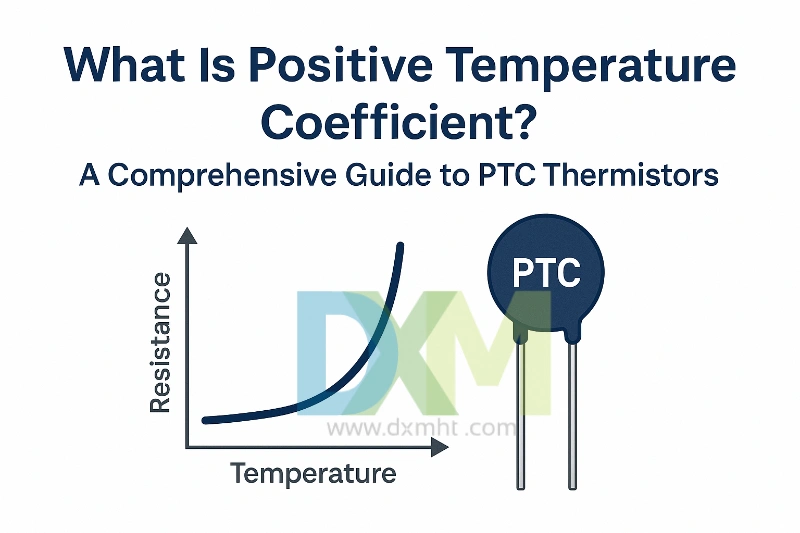
What Is Positive Temperature Coefficient? Expert Guide on PTC Thermistors
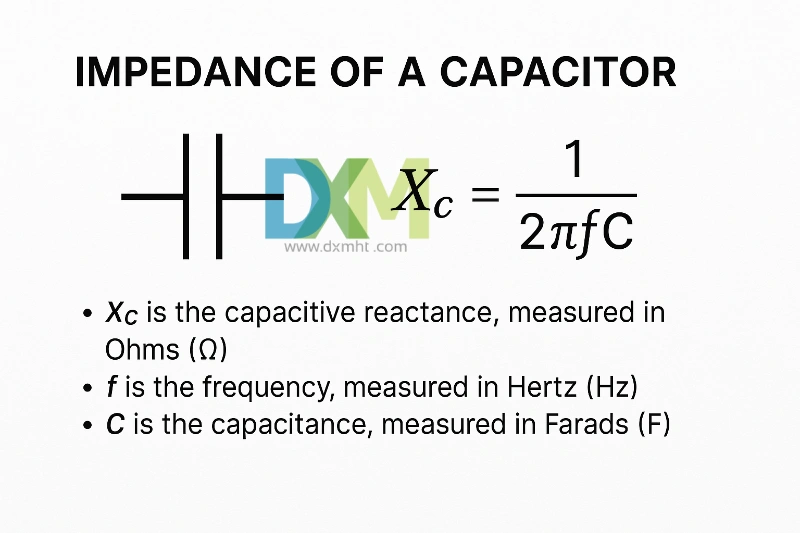
How to Find Impedance of a Capacitor: Guide for Professionals
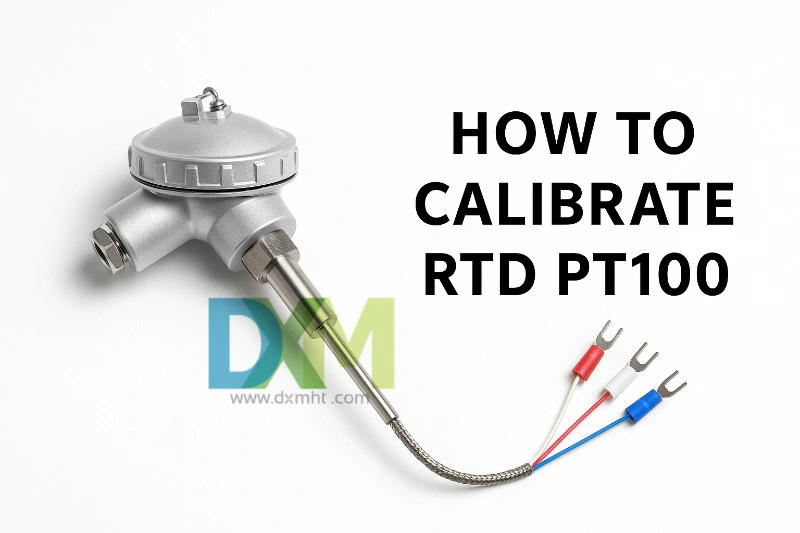
how to calibrate rtd pt100?
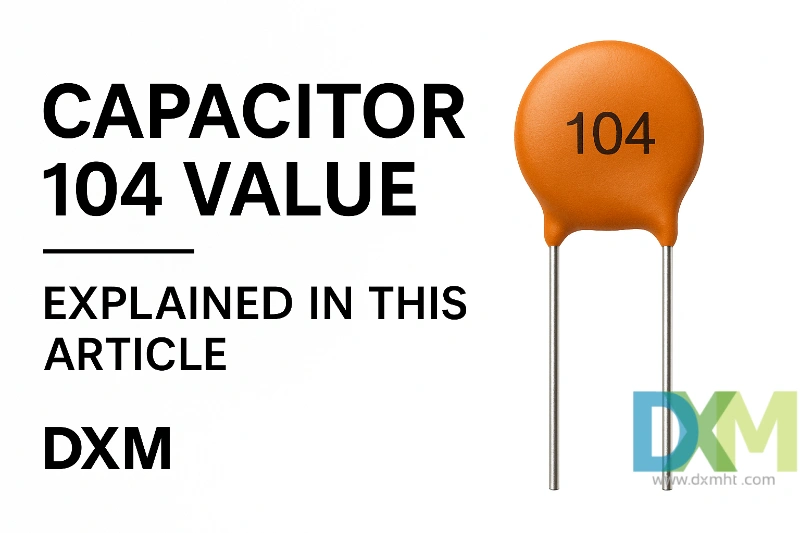
Capacitor 104 Value: Essential Guide for Electronics Professionals
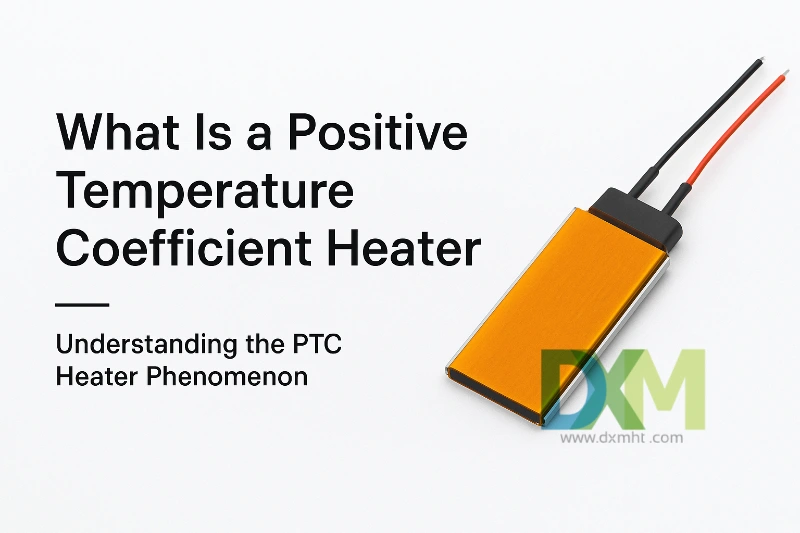
Positive Temperature Coefficient Heater: An Essential Guide of PTC Heater
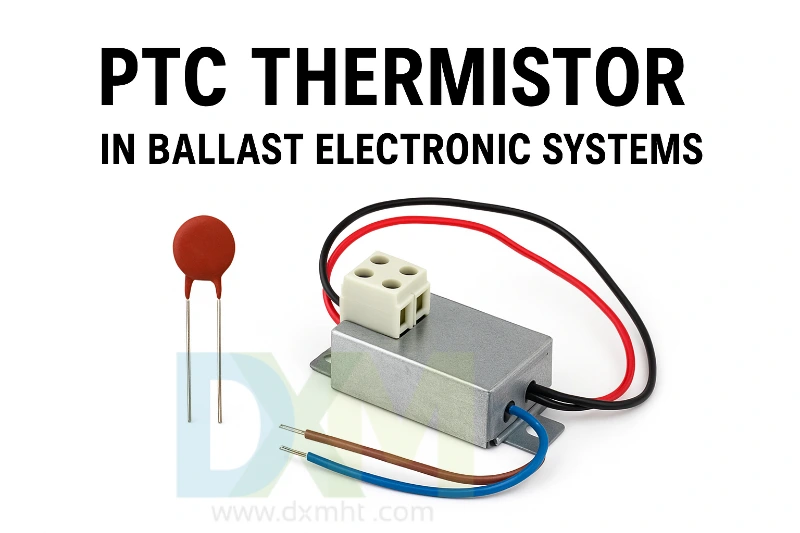
What is an Electronic Ballast PTC Thermistor? Insights from DXM.
Price and Payment
Do you offer bulk purchase discounts?
Yes, we offer bulk purchase discounts; the specific discount rate depends on the order quantity and cooperation method.
Price
The price will be quoted in US dollars.
1) For small order quantities and small packing, normally our quotation is based on the ex-works price. The cargo will be delivered by courier after being finished normally.
2) For bulk orders and large volumes, normally our quotation is based on the FOB price. Please inform us of your destination seaport and estimated quantity, and our representative will quote you the C&F or CIF price accordingly. If you feel our freight is higher than your expectation, you can recommend your shipping company to us. Our principal is looking for a shipping company with a good reputation that offers competitive freight costs and can deliver your cargo promptly.
Payment Terms
There are a number of different payment methods that can be used when you deal with us. Two are mostly used: T/T payment in advance for small values and irrevocable L/C at sight for large values.
Logistics
Is your logistics and distribution service reliable?
Yes, we cooperate with a number of well-known logistics companies to ensure the timeliness and reliability of logistics and distribution services and provide you with a satisfactory distribution experience.
Customized Services
Custom-made sample/order
SHENZHEN DXM TECHNOLOGY CO., LTD. are structured by high-tech talents from famous university
in China and accompanied with a batch of ceramic-sensitive components experts and technology
specialist, have powerful R&D and technology capabilities.DXM is one of a few manufacturers
master core production technology of ceramic-sensitive components in the world.
Samples and orders can be custom-made per customer’s requirements, as below:
1. Application environment of product
2. Required specifications or technical parameters
3. Reference sample
4. Reference drawing
You may also like
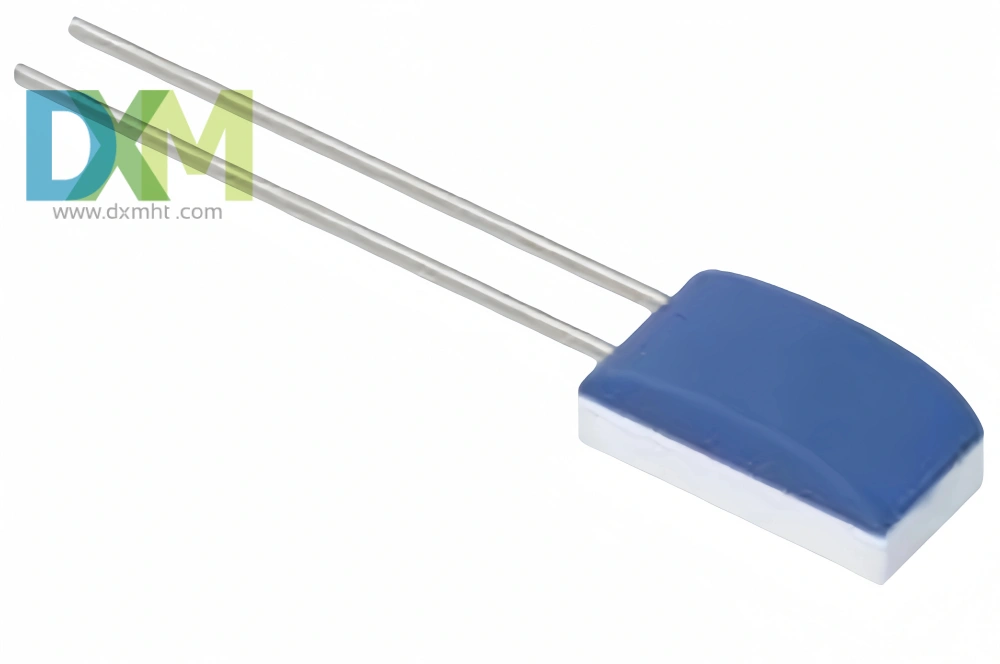
PT100 Temperature Sensor - High Accuracy for Industrial Applications
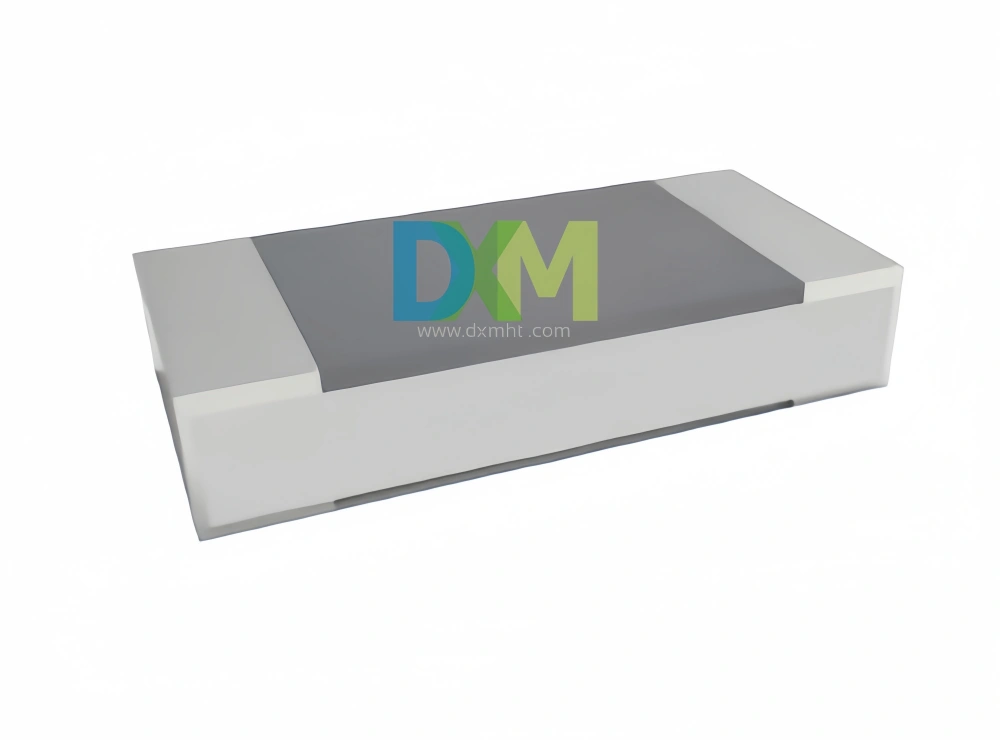
Sensor PT100 SMD Introduction
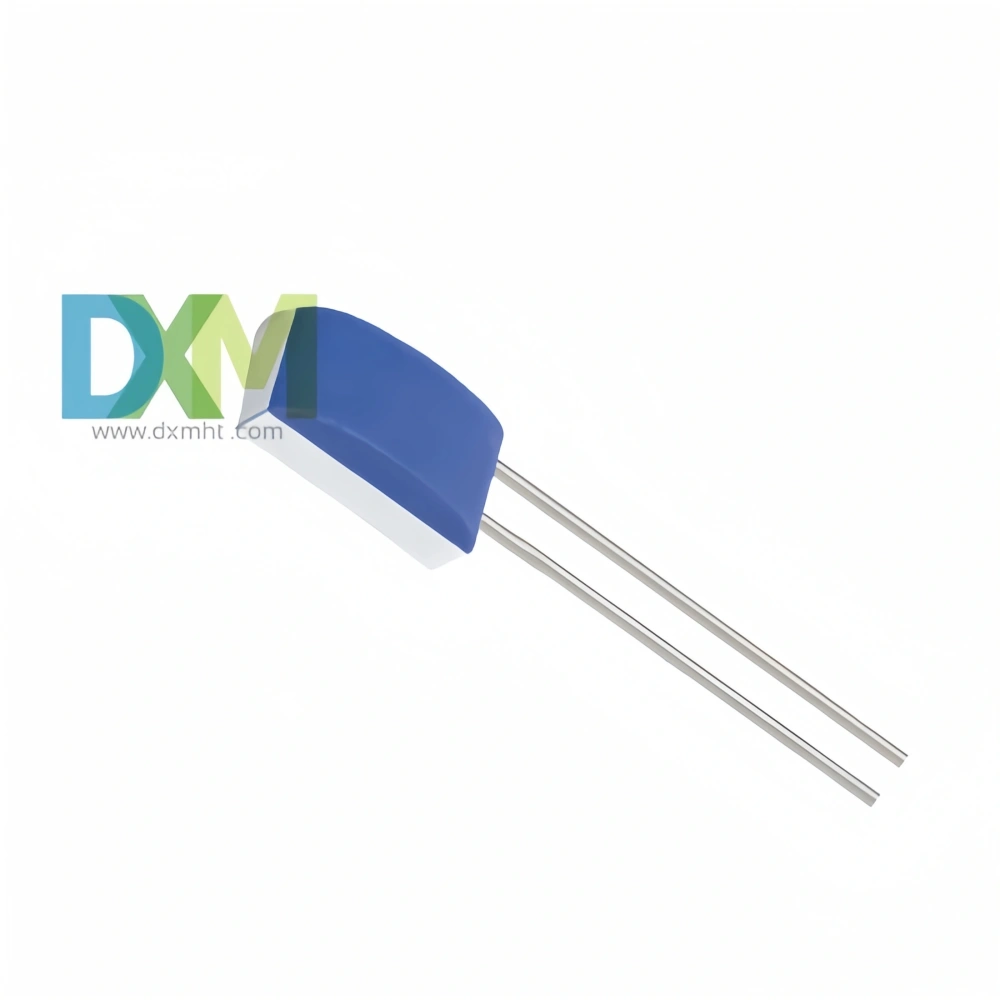
RTD Temperature Sensor PT1000: Precision Temperature Sensing for Various Industries
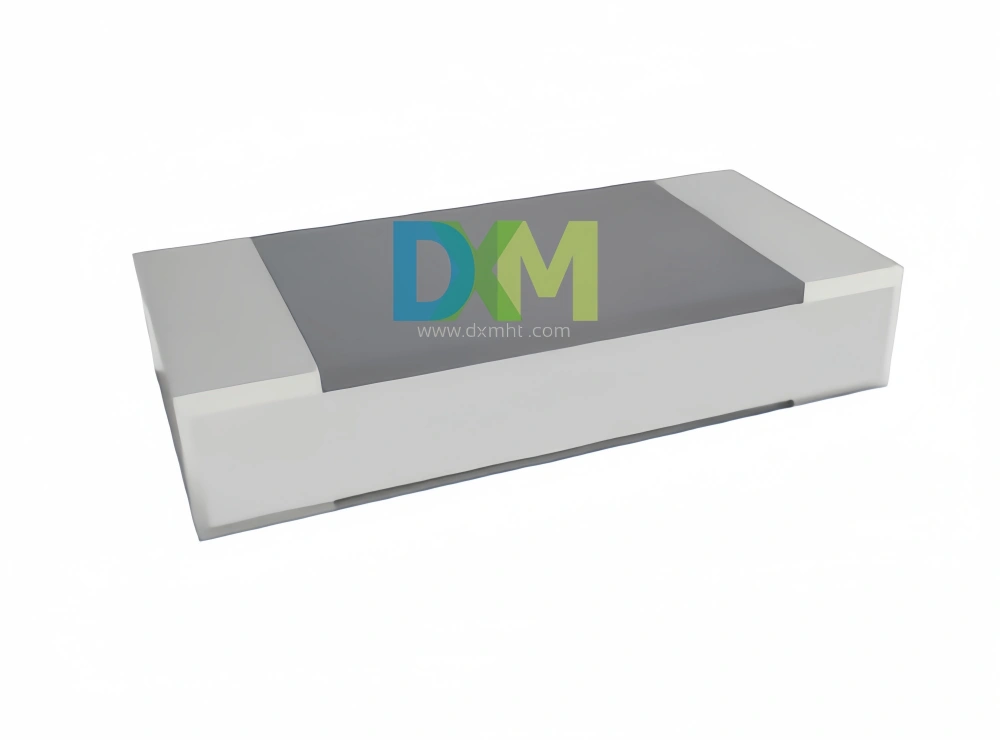
Sensor RTD PT1000 SMD for Precision Temperature Measurement
Get in Touch
Discover premium thermistors, sensors, and resistors tailored to your needs.Our dedicated team of experts is available to assist with product selection, technical queries, and after-sales service. Contact us for custom solutions and experience exceptional customer support.
© 2025 DXM | All Rights Reserved.
Scan QR Code
Whatsapp: +8618927361658
Shenzhen DXM Technology Co., Ltd.
DXM PTCNTC
Shenzhen DXM Technology Co., Ltd